Choosing Adjustable Guide Rails That Improve Uptime and OEE
Mar 3, 2022
If you’re looking for changeover and container handling solutions that provide big line efficiency with small line flexibility, adjustable guide rails are one of your best options.
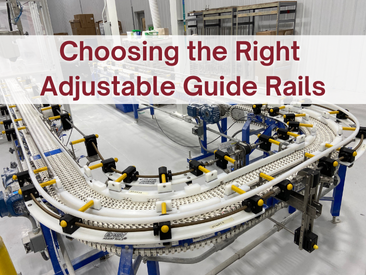
Adjustable guide rail solutions increase your flexibility to handle multiple container sizes and shape, while reducing changeover time. Throughput and handling performance can also improve with adjustable guide rails, particularly for hard-to-handle containers and with challenging line configurations. The best adjustable guide rails deliver fast, repeatable set ups that eliminate fine tuning and variables that create downtime or poor production. Depending on the type of system, guide rail changeovers can be cut from hours to a few minutes or even seconds. The most efficient systems are easy-to-use and reduce the need for skilled labor to changeover.
Return on Investment
Most users see a return on their investment with increased uptime and improved OEE in less than a year depending on the frequency of changeovers and line configuration. Labor efficiency is also improved for most users. For the majority of Septimatech customers, ROI of less than a year is realized with three, 30-minute changeovers per week.
Several design factors impact the changeover efficiency of adjustable guide rails, including the level of automation, type of actuators, and adjustment flexibility. Available solutions range from manual, centrally adjustable systems that control sections of guide rail from a single location to fully automated systems. The most efficient and cost-effective manually adjusted systems typically have a hand wheel or crank equipped with digital counters that allow precise, repeatable adjustments — either single-sided or dual-sided.
Fully automated solutions can be integrated with existing controls to provide recipe-driven, one-touch changeover. Integration with existing controls and management systems provides valuable data for OEE transparency, traceability, and quality control. Guide rail changeover time typically is reduced to seconds.
Precise, repeatable adjustable guide rails that properly maintain position during backpressure improve container control and throughput by eliminating shingling, jamming, popping up and tipping. Some systems can be further customized to provide multiple vertical and horizontal adjustments that improve handling difficult to convey containers. Corners, crossovers, accumulation and funneling areas can create handling challenges and reductions in line performance. Depending on the type of adjustable guide rails, challenges in these areas can be eliminated to improve throughput.
Not all Adjustable Guide Rails are created equal.
One of the most crucial components on Adjustable Guide Rails is the actuation system. The actuation system controls adjustment, impacts container handling capabilities, and helps provide structural integrity to the system. Here are some of the differences between two of the most commonly used systems, mechanical and pneumatic actuators:
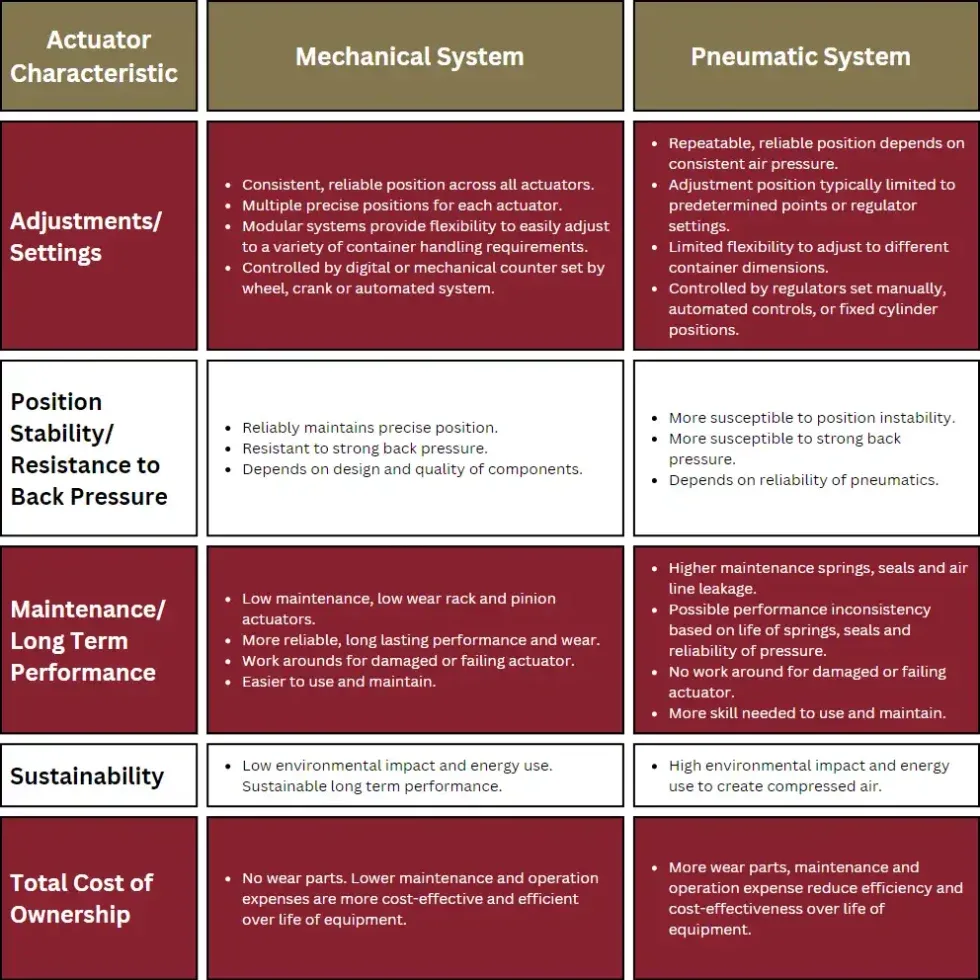
A container handling expert can help you get the best adjustable guide rail solution for your unique production needs and budget. To help you evaluate solutions and discuss options with your solution provider, here are some questions you should ask:
What are my Changeover Requirements?
- How many changeovers do you make?
- What are your goals?
- How do you expect changeover frequency to change in the future?
What should I consider with my Production Environment and Line Layout?
- Is the system scalable and easy-to-reconfigure as needs change?
- Are materials wash down capable if needed?
- Are sections of your line overhead or hard to access?
- What are your container handling requirements?
- What is the footprint of components?
How easy is this system to use?
- Is the system easy to understand and use?
- How much adjustment and fine-tuning is needed during setup?
- Does it meet your adjustment requirements?
- How many adjustment points are required?
- What is the changeover and setup process and time?
How much labor is involved in the maintenance of the system?
- Are components easy-to-maintain and troubleshoot?
- What is the mean-time-between-failure of components?
- What is required for supporting systems, such as air or electricity?
- How much training is needed?
- What happens if actuator goes down?
- Can repairs be made on-site?
How easy will it be to install?
- Are brackets and adjusters easy-to-install and add on to existing lines?
- Are brackets and adjusters robust?
- What supporting systems need to be installed?
- Are components reusable as line configurations change?
- Can in-house labor be used to help manage installation costs?
What will be our Total Cost of Ownership?
- What are upfront, maintenance, energy, and operations costs?
- What is your estimated cost and downtime per changeover?
- What is your estimated product loss from improper handling?
- What are desired throughput goals?
- What is the expected lifetime of components?
What are my Container Requirements?
- What are material handling requirements for your containers?
- How frequently are they changed over?
- Is the system flexible to meet needs for future containers?