Create a Competitive Advantage by Improving Changeover Efficiency
May 9, 2023
Improving Packaging Changeover Efficiency is one of the Most Powerful Ways for you to Build a Competitive Advantage. The International Society of Automation (ISA) estimates manufacturers lose 5 to 20 percent of their productivity due to downtime.
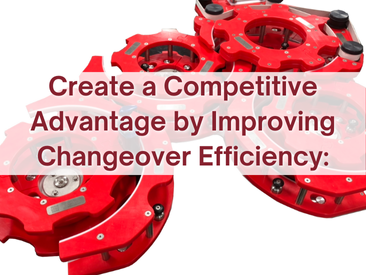
Furthermore, ISA estimates approximately 80 percent of manufacturers are unable to accurately estimate their downtime, even for planned stoppages like changeovers. For many manufacturers, it can take up to an entire shift for equipment setup and an additional few hours of adjustments before a line is running at full capacity. Any time your line is not producing products at optimum levels, even during planned downtime, you are losing significant money— tens of thousands of dollars per changeover.
Higher production run time and lower operating costs are only part of the strategic benefit of improving your changeovers. Increased changeover efficiency also improves line flexibility, response to market demands, and Overall Equipment Effectiveness (OEE). Simplifying changeovers so they are faster, less strenuous, and more productive also improves labor productivity and creates an ergonomically safer, more pleasant work environment. Manufacturers with fast, repeatable changeover processes and solutions that are intuitive, easy-to-use and more flexible gain greater ability to adapt to changing business conditions. This adaptive advantage made a significant difference for companies with more efficient changeovers during recent market and production challenges created by the COVID pandemic, labor shortages, supply chain issues and inflation pressures.
Where Do You Start?
Improving changeover time can be daunting. Some of the most common challenges manufacturers cite include:
- Adequately measuring changeover time and related costs
- Identifying the most cost-effective opportunities and investments for improvement
- Mistake proofing
- Skilled labor shortages
- Eliminating adjustments after setup
- Parts storage and transportation
- Sanitation and line clearance
- Line layout and space restrictions
- Need for more ergonomic change parts solutions
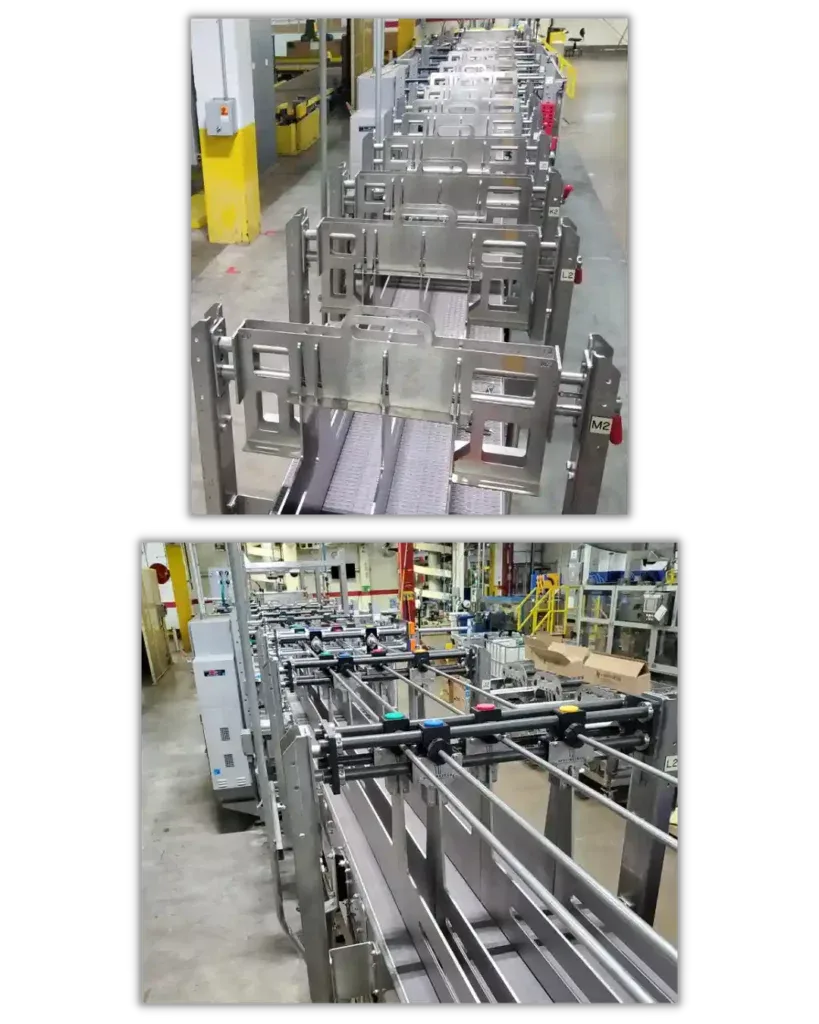
When developing a plan, collect as much data as possible about all phases of your changeovers, from line clearance and cleaning through machine setup to adjustments required to get your line running at full capacity. Leverage the wisdom of your more experienced line operators and maintenance technicians. They are frequently aware of common problem areas and can help identify opportunities. Also choose an experienced changeover and container handling expert that will collaborate closely with you to provide solutions with your strategic goals in mind.
The most cost-effective and efficient changeover solutions improve common OEE measures — uptime, time producing quality product, and time a line runs at peak performance. Lean manufacturing experts emphasize the importance of removing variability from changeovers before focusing on speed. Accurate, repeatable setups reduce fine-tuning after container switches and improve time to reach peak production. Outcomes are more predictable and reliable, making them easier to measure and continuously improve. Additionally, faster changeovers are frequently a byproduct of reduced variability and easily repeatable setup.
For example, Quick Change Parts ensure one-way installation for fast, simple, repeatable changeovers that eliminate operator variables. Custom-engraving and color-coding provide fast, easy identification. Thoughtful design, surface finishing and material choices can also facilitate easy cleaning, storage, and transportation. Standardizing on common solutions across your lines promotes faster changeovers, as well as fewer errors, reduced training and less variance among different operators.
Adjustable Guide Rail Solutions:
Adjustable changeover solutions for guide rails and multiple conveyance lanes allow one person to adjust large or difficult to access sections of a line from one location, reducing setup time from hours to a few minutes or even seconds. Labor can be reallocated to other production or changeover needs.
Improved container control reduces unplanned downtime caused by shingling, jamming, popping up and tipping. Solutions range from manual, centrally adjustable systems to fully automated systems that integrate with existing controls and provide valuable data for OEE transparency. The most efficient and cost-effective manually adjusted systems typically have a hand wheel or crank equipped with digital counters that allow precise, repeatable adjustments — either single-sided or dual- sided. Some manual systems can be upgraded to provide multiple vertical and horizontal adjustments to fit a wide range of containers.
Change Part Carts:
Change Parts Carts keep parts organized and easy to identify and make them easy to transport and clean. Some changeover carts are user-configurable for cost-effective versatility, while others can be customized to match your unique changeover processes for ultimate efficiency. Simplifying changeovers so they are faster, less strenuous, and easier to manage increases productivity and creates a safer, more pleasant work environment.
Changeover Efficiency—The Sum of All the Parts
Because changeovers are a complex end-to-end process, it’s easy to forget sometimes that small efficiency improvements can often be implemented quickly and cost effectively with great results. Eliminating just one step in a frequently performed task or changing how you store and transport change parts can have a huge impact on packaging line productivity. Incremental improvements across one or multiple lines, either through process improvements or investment in more efficient changeover solutions, add up exponentially to create significant competitive advantages.
The keys to efficient changeovers that provide a competitive advantage include:
- Complete changeover tasks without stopping production.
- Eliminate variables that create errors and inconsistent performance.
- Invest in changeover solutions that eliminates steps, reduces potential errors, and creates more uptime.
- Eliminate fine-tuning after start.
One of the things we sometimes hear at Septimatech when we’re working with a new customer is “that’s only one part of my changeover, why should I make that investment?” Foremost is that Septimatech’s changeover solutions tick all the boxes for achieving more uptime and improved throughput when you do a line changeover from one product size to another. They eliminate variables, and fine tuning. You can simultaneously changeover different parts of your line with reduced labor and disruption. They reduce errors and are fast. That’s value and return on investment that our customers realize almost immediately.