Three Key Ways Pharmaceutical Manufacturers Gain an Edge by Collaborating with Changeover and Container Handling Specialists
Oct 6, 2023
Introducing new products and making improvements to packaging line performance can present multiple challenges for pharmaceutical manufacturers. Maintaining compliance, product integrity, sanitation, and traceability requirements, while also enhancing efficiency and productivity requires thoughtful planning and design. Keys to success frequently depend on changeover efficiency and container handling performance.
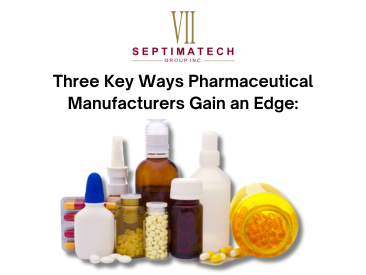
Here’s a look at how collaborative relationships with changeover and container handling providers provide significant value for pharmaceutical manufacturers in three key ways:
1. Collaborative Relationships
There are huge variances in pharmaceutical packaging environments, depending on products, clean room standards, regulations, compliance protocols and how different companies approach those challenges. The most effective solution design and construction materials vary from one pharmaceutical packager to the next and sometimes from plant to plant depending on packaging requirements, environment, and regulatory compliance. Working directly with pharmaceutical packagers to understand their specific goals, challenges, and requirements is key to providing solutions that meet their requirements and enhance performance. A common mistake made by some change parts providers that ultimately leads to longer lead times and diminished performance is relying on experience and expertise alone without collaborating directly with their pharmaceutical customers.
Strong communication and collaboration combined with experience helps mitigate risks and leads to quality solutions. More so than most industries, pharmaceutical manufacturers may need to document materials of construction for regulatory compliance and certification. Surface finish, environment, and potential sources of contaminants, such as airflow, dust, cleaning solutions, and possible product spillage must be considered in the design of changeover and container handling solutions across the line. Packaging aesthetics are also an important consideration for pharmaceutical companies, which frequently require non-marking and anti-scuff container handling solutions.
Collaboration
New change part technology exists to help us solve issues that couldn’t be overcome in the past. A change parts specialist can provide enhancements that aren’t frequently available in OEM change parts or possible in older systems. This could be increased functionality and flexibility, or solutions for complex container control and positioning, new materials, or fast, repeatable changeovers.
For example, product orientation and container handling are also frequently important to ensure proper sensor scanning, filling, and product counting for traceability requirements.
2. Hygienics and Prevention of Cross-Contamination
Solutions that prevent cross-contamination and meet hygienic requirements are the highest priority of any changeover and product handling solution. It is the most common requirement Septimatech helps pharmaceutical companies achieve when they upgrade their packaging lines or introduce new products.
Construction materials, engineering, and finish are primary design factors in ensuring product integrity and performance. Whether ingredients are liquids, tablets, or powders, engineering solutions that prevent pooling or trapping of product ingredients and cleaning chemicals is crucial to prevent cross-contamination. If a tablet, powder, or liquid ingredient spills it becomes a source of cross-contamination and the product can’t pool or be trapped on or in the change parts solution or easily cleaned to support hygienic requirements. All possible contaminants must be directed downward to the floor. Similarly, airflow, dust, cleaning solutions, and other possible contaminants must be directed toward the floor.
Hygienics:
Changeover and container handling providers with pharmaceutical experience and expertise can design solutions across the line that are self-clearing and self-washing. The type of materials and finish—such as electropolished stainless steel, Delrin, or other inert plastics—are crucial to maintaining product integrity and preventing cross-contamination while meeting FDA and hygienic requirements.
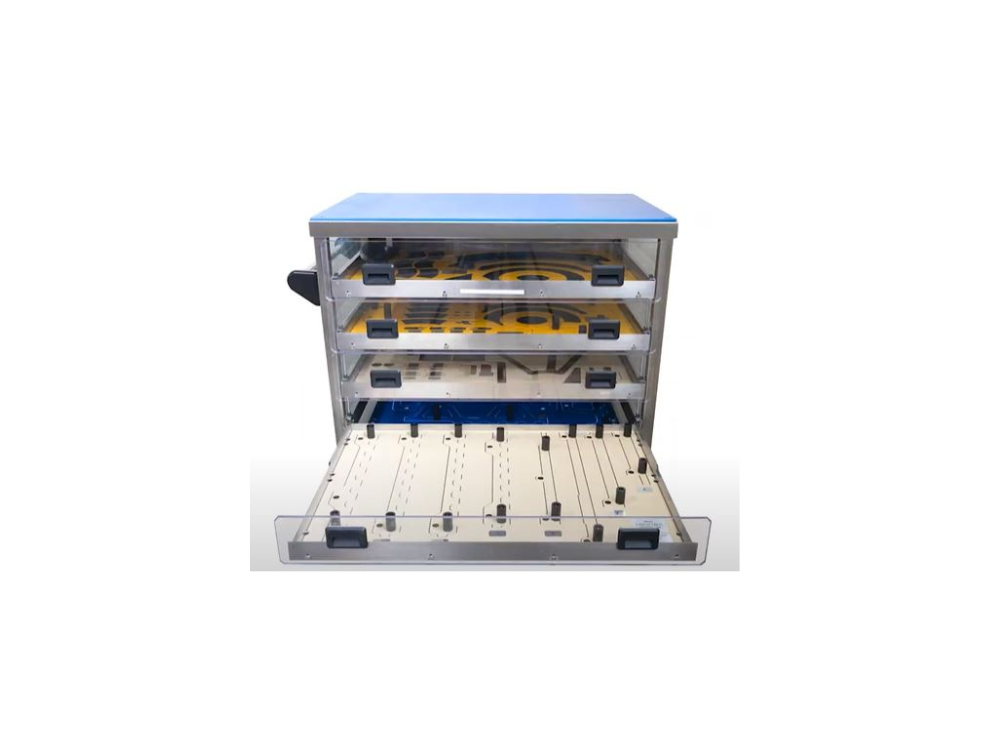
Additionally, experienced container handling specialists are frequently asked to design enhanced solutions that eliminate touch near ingredients and container openings in critical filling and capping areas of the line. Septimatech provides a wide range of container handling and changeover problem solving assistance and solutions to pharmaceutical manufacturers. All solutions are tested and simulated to ensure high performance results, prevent unexpected errors, and enhance productivity.
3. Reducing Risks and Increasing Productivity with Efficient, Repeatable Changeovers
Environmental and product complexity tend to make changeovers longer in pharmaceutical manufacturing than in other industries. The risk with lengthy changeovers is an increased likelihood of errors that lead to cross-contamination, product loss, compliance issues and of course, lost production and higher costs. By creating more efficient, repeatable changeovers, pharmaceutical manufacturers reduce potential errors, mitigate risks, and improve quality control.
Simplifying changeovers so they are faster, more precise, and less strenuous improves labor productivity and creates a safer, more pleasant work environment. Labor and time can be reallocated for other tasks such as equipment maintenance, process improvement, operator training, or quality control and compliance measures.
Improving changeover efficiency also typically increases productivity and line flexibility, which leads to more effective inventory management and faster response to evolving business and customer demands.
Pharmaceutical manufacturers...
...who received the most value from changeover improvements typically focus on:
- sanitation and line clearance
- mistake proofing through standardized, repeatable processes
- eliminating adjustments after changeover and setup
- efficient parts storage, cleaning, and transportation.

The most cost-effective and efficient changeover solutions improve on common OEE measures — uptime, time producing quality product, and time a line runs at peak performance. Lean manufacturing experts emphasize the importance of removing variability from changeovers before focusing on speed. Accurate, repeatable setups reduce fine-tuning after container switches and improve time to reach peak production. Outcomes are more predictable and reliable, making them easier to measure and continuously improve. Additionally, faster changeovers are frequently a byproduct of reduced variability and an easy, repeatable setup.
For example, change parts that ensure one-way installation for fast, simple, repeatable changeovers eliminate operator variables. Custom-engraving and color-coding provide fast, easy identification. Thoughtful design, smooth surface finishing and inert material choices prevent cross-contamination, and simplify sanitation, storage, and transportation. Standardizing on common solutions across your lines also promotes faster changeovers, less errors and reduced training time.
Specialized pharmaceutical change parts carts ensure sanitary storage and keep parts organized and easy to identify, transport, and clean. Change parts carts are one of the most crucial tools for pharmaceutical companies to reduce errors, damaging or losing change parts, preventing cross-contamination, and improve efficiency. Most pharmaceutical companies have specific and frequently unique cart design requirements, from materials and surfaces to how parts are oriented and stored to maintain sanitary standards. To increase efficiency and reduce cross-contamination risks, some pharmaceutical manufacturers will use two carts —one for storing the sanitized parts and one to transport and clean used, dirty parts.
Changeover solutions for clearing the line of excess product and guide rail adjustment allow one person to setup large or difficult to access sections of a line from one location, reducing time from hours to a few minutes or even seconds. Adjustable guide rails with precise adjustments reduce container/bottle tipping, shingling / jamming and accidental spillage of product and prevent trapping and pooling of liquids, tablets, and other ingredients