Blogs
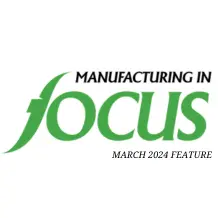
Manufacturing In Focus – March 2024
Septimatech was recently featured in the March edition of Manufacturing in Focus. To read our article for free, click on the snippet of the magazine below:
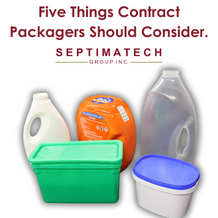
Top 5 Areas To Focus Your Attention as a Contact Packager.
Being the Best Partner to Contract Packagers Starts with Helping them be the Best Partner for their Customers. Performance, flexibility, and turnaround time are a few of the most powerful ways contract packagers build a competitive advantage. But where do contract...
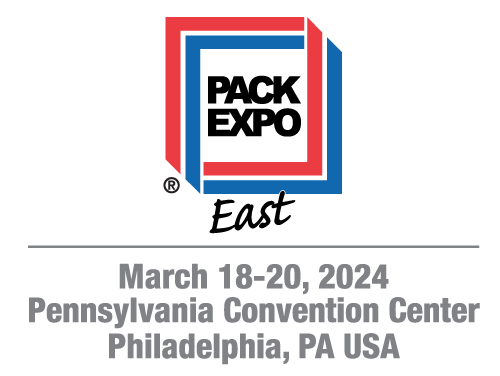
Products on Display – Pack Expo East 2024
Need to Improve Efficiency and Increase Production with Less Labor and Downtime? See Septimatech Changeover and Container Control Solutions atPack Expo East 2024: Visit us at Booth 1255, March 18th - 20th at the Pennsylvania Convention Center in Philadelphia, PA....
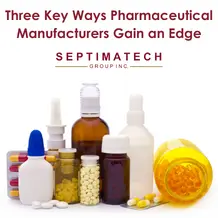
Three Key Ways Pharmaceutical Manufacturers Gain an Edge by Collaborating with Changeover and Container Handling Specialists
Introducing new products and making improvements to packaging line performance can present multiple challenges for pharmaceutical manufacturers. Maintaining compliance, product integrity, sanitation, and traceability requirements, while also enhancing efficiency and...
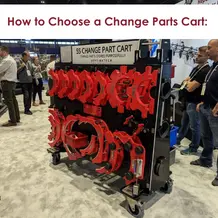
Choosing the Best Packaging Change Parts Storage Solution for Your Needs
Change Parts Carts are a cost-effective way to simplify packaging changeovers and improve parts management.They help make changeovers more efficient, faster and less strenuous. They also reduce risk of parts damage and loss while improving storage capacity. To get the...
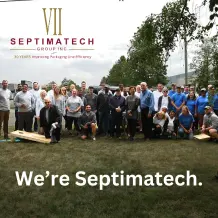
We’re Septimatech—Trusted Changeover and Container Handling Solutions for Productive Packaging Lines Worldwide
Team Septimatech has a proven record for helping companies worldwide make their packaging lines more productive through more efficient changeovers and improved container handling. Whether you need a single change part, or a large-scale changeover and container...